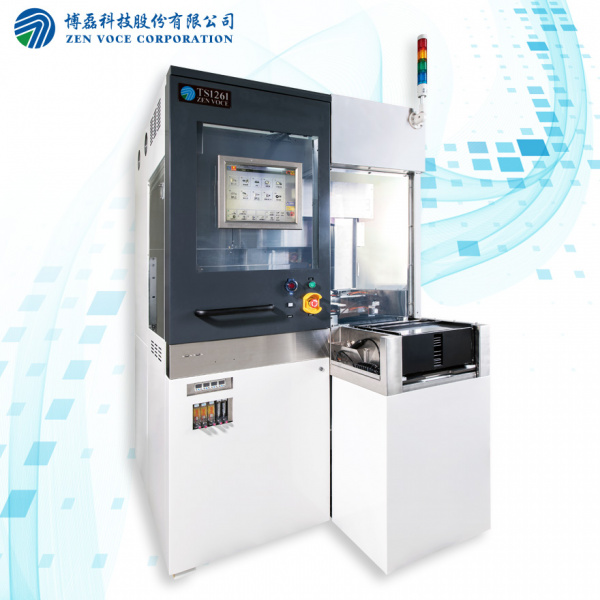
Fully Automatic Dual Spindles Wafer Dicer- TS1261Fully Automatic Dual Spindles Wafer Dicer- TS1261
Equipped with a short spindle, the space planning of the gantry structure has been optimized, reducing the footprint of the machine by 10% and narrowing the width by 20%. Additionally, all maintenance can be performed from the front of the machine, eliminating the need for side access. This includes the maintenance area, resulting in a 20% reduction in overall workspace (layout) area. It is especially suitable for factories that require the installation of multiple 300mm diameter cutting machines. (Compared to our TS1260 model)
Product Specifications
Intuitive Operator Assistance
Through an LCD touchscreen panel, operators can perform calibration and reading tasks while viewing the microscope screen. Additionally, graphical charts of machine status and MTBA (Mean Time Between Assists) provide a visual representation of the machine's operating condition. Instructions for handling abnormalities are also displayed on the screen, assisting in troubleshooting operations.
Options to Suppress Fine Particulate Dust
Fluid Nozzle for the cutting section. Fluid Nozzle for the spinner section. Worktable water curtain to prevent hardening caused by drying particles. Powerful exhaust duct (spindle).
Reduction in Maintenance Area
From daily operations to maintenance tasks, everything can be performed from the front. When arranging multiple machines side by side, the reduced maintenance space on the sides allows for the placement of 6 TS1261 machines, compared to the previous 4 TS1260 machines.
Workpiece Cutting Process Flowchart
Material pick-up arm retrieves the workpiece from the material box and transfers it to the pre-alignment stage. After center alignment on the pre-alignment stage, the lower arm moves the workpiece onto the worktable. Cutting process takes place. The upper arm transfers the workpiece to the centrifugal cleaning stage. Cleaning and drying are performed. The lower arm returns the workpiece to the pre-alignment stage. The material pick-up arm returns the workpiece to the material box.
Standard Features
Auto Kerf Check for automatic kerf calibration. NCS (Non-Contact Setup) for non-contact measurement of blade height. Blade Broken Detector for detecting broken blades. Fluid Nozzle for fluid application.
Optional Features
Hardware: In-line Dressing for online blade grinding, enhanced dust cleaning (Class 100), Laser Kerf Alignment with special CCD, CO2 system (external attachment), and chemical mixing equipment (external attachment).
Software: Laser Kerf Alignment, SECS/GEM, and other customized software functionalities.
Specification |
Unit |
TS1261 |
|
(1.2/1.8/2.4Kw) |
|||
Max. workpiece size |
mm |
Φ300/Φ200 |
|
X-axis |
Cutting range |
mm |
310/210 |
Cutting speed |
mm/sec |
0.1-1,000 |
|
Y1、Y2-axis |
Cutting range |
mm |
310 |
Index step |
mm |
0.0001 |
|
Index positioning accuracy |
mm |
0.003/310 |
|
mm |
0.002/5(Single error) |
||
Z-axis |
Max. stroke |
mm |
14.2(For φ2”blade) |
Moving resolution |
mm |
0.0000003(24bit) |
|
Repeatability accuracy |
mm |
0.001 |
|
ϴ-axis |
Max. rotating angle |
deg |
380 |
Spindle |
Rated torque |
N.m |
0.27 |
Revolution speed range |
rpm |
6,000-60,000 |
|
Machine dimensions (W x D x H) |
mm |
1,250 x 1,600 x 1,890 |
|
Machine weight |
kg |
2,150 |