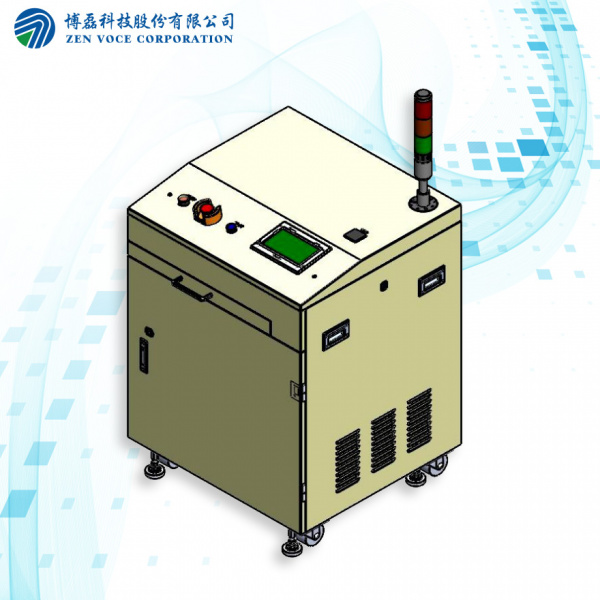
Semi-Automatic UV Curing Machine – UV3612Semi-Automatic UV Curing Machine – UV3612
The UV-3612 is a semi-automatic UV adhesive remover with LED technology. It is designed for the delamination process of film-coated products. It offers lightweight and easy operation, complete adhesive removal, and easy maintenance as its key features.
Product Specifications
Features:
- This machine is designed as a floor-standing UV adhesive remover.
- The light source shines from bottom to top, ensuring that the film remains in place after adhesive removal and curing.
- Manual placement of materials in a drawer-style compartment allows for one-click adhesive removal operation by pressing the START button.
- The drawer-style lightbox assembly is convenient for maintenance and component replacement.
- The light source consists of a surface light with 729 LED lamps of wavelength 365nm. It has a long lifespan, uniform illumination, does not generate ozone, instantly turns on without warm-up time, and consumes minimal power. The light source turns off when in standby mode.
- Built-in light intensity sensor detects the light source intensity in real-time and displays it on the human-machine interface, along with the total accumulated irradiance for adhesive removal.
- The control system utilizes a PLC (Programmable Logic Controller) in conjunction with a human-machine interface. Adhesive removal control is based on setting the total accumulated irradiance (not time-based). The adhesive removal time is adjusted and displayed on the control panel according to the accumulated irradiance. The system also features automatic compensation for diminishing light source intensity to avoid insufficient or excessive adhesive removal.
- The adhesive removal chamber has a nitrogen purge function that enhances the adhesive removal effect when activated.
- Equipped with over-temperature protection, the machine automatically turns off the lights in the adhesive removal chamber when it becomes overheated.
- Lamp bead failure detection function displays a message on the human-machine interface panel in case of lamp board malfunction.
- The human-machine interface has a built-in irradiance calibration screen, allowing users to perform irradiance calibration procedures using a UV radiometer standard. Users can perform calibration themselves.
- Built-in exhaust system for temperature stabilization and heat dissipation.
Machine Operation:
- Adjust the AIR pressure to 3-5 kg/cm² before use. The factory setting for the cooling system activation temperature is 35°C, which is the optimal startup temperature. Setting it too high may result in machine damage, while setting it too low may not achieve the required irradiance for operation. The temperature for forced light-off is set to 45°C to protect the lamps from prolonged overheating, which can lead to damage.
- Turn on the main power and press the POWER button to start the power (red light illuminates).
- Use the human-machine interface to set the accumulated irradiance value for the desired exposure time. Pull out the drawer and place the wafer chip inside to begin operation.
- Place the delamination film on the tray (use different trays based on material size), close the drawer, and press the START button. The process indicator light will flash blue.
- The accumulated irradiance value for exposure can be changed according to the UV film requirements. Once the exposure is complete, the button indicator light will turn off.
- Pull out the drawer and remove the wafer chip, then proceed with the next process operation.
- If there is any malfunction or safety concerns during the operation, stop the operation, resolve the issue, and then restart following the above procedure.
- When not in use, press the POWER button (light turns off) and turn off the main power to avoid unnecessary energy consumption.
Technical Specifications:
Machine Model |
UV-3612 |
Frame Dimensions |
6、8、12 inches(Manufactured according to protocol specifications) |
Light Source: |
consists of 9 light panels, with each panel containing 81 LED bulbs. |
Light Source |
UV-A 365nm |
Light Source Intensity |
Factory set to 100mW/cm2 (measured using our company's light meter) |
Debonding Irradiation Distance |
Approximately 25 mm |
Maximum Irradiation Area |
350mm*350mm |
Uniformity of Intensity |
Within 10% in the 320mm320mm irradiation area |
Total Power Consumption of Light Panels |
Approximately 2 KW |
Lamp Lifespan |
It is recommended to replace the light panels when the accumulated usage time reaches 10,000 hours or 2 years to achieve optimal debonding results. (Actual lifespan may vary depending on individual usage conditions. The above values are suggested references, not guaranteed values.) |
Power |
Single-phase AC 220V 50/60Hz, 20A |
Power Supply |
IN: AC 220V OUT: DC36V, 240W *9 sets |
Operating Interface |
7-inch color HMI (Human-Machine Interface) |
Controller |
Programmable Logic Controller (PLC) |
N2 Purge Function |
Supports N2 Purge function to enhance debonding effectiveness |
Heat Dissipation and Exhaust |
Aluminum fin heat sink + Cooling fan (1/2HP, 18CMM, 75mmAq) |
Exterior Dimensions |
730(W)㎜*680(L)㎜*1000(H)mm |
Weight |
Approximately 150 KG |